OEM TPU
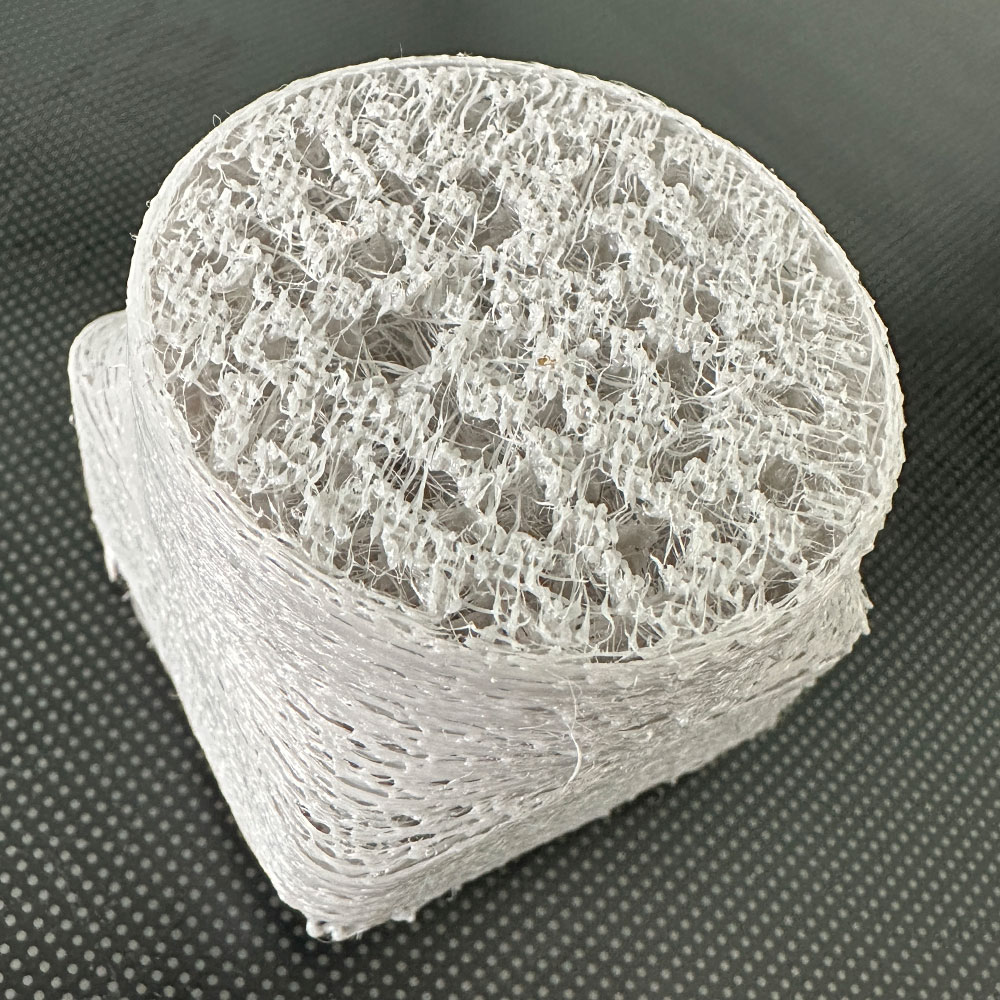
Labwork – Various Filaments
Filament types, brands etc. a nightmare of a problem to have. Which filament to purchase, what works best on the 3d printer I own? What to do when you’re just starting out? Cut to the point, purchase, use what you can in context, however, when push comes to shove… Ender Series, Prusa, Makerbot all great choices for novices or beginners. Start with an eBay ‘parts’ printer, this might help cut down cost or refurb’ed. In time, as you learn the in’s and out’s of 3d printing, overcoming fine-tuning issues and filament extrusion/application will be key.
Regardless of product make/structure, the fine-tuning the nozzles, stability of the machine, drive system, adhesion and filament… Filament might be the easiest to swap out, may be the nozzle (noting various nozzle sizes, most default include .4mm) and for those hobbyist, the drive mechanism, bed/build plates etc. Filament might just be an easy swap with a catch.
Like most things, filament comes with it’s own issues – additional research is required, fine tuning and testing depending on choice of 3d printer. Let’s talk shop, filaments… retraction (later, future post). Listen, if purchase power is a problem, meaning if you have the money, first, buy what you can afford, especially those starting out in the 3d printing hobby… Do what you can to make ‘it work’. Making it work, meaning so that you can test, test, and retest. It’s a process of elimination, elimination of problems over time. Better filaments, better results. There have been many times when testing, in fact, I might venture to say, problems are related to cost of filament and the length of time it takes the user to move from the cheap ‘stuff’ to the final working filament. After all, at least in my filament finding (tersting) days, more often than not, filament testing became cost to throw-away, ‘what not to do’. So, yes, a healthy dose of testing is needed; failure as well. That said, I would be remise not to shine a spotlight on the value of the article; which is saving you money on filaments, pieces, parts and cost to print etc. The punchline, buy and match OEM (Original Equipment Manufacturing) filaments. I have a Creality ‘shop’, thus, I use Creality filaments – Creality TPU (Thermoplastic Polyurethane) Filament.
Lately, we’ve been looking branch out a bit, as we’ve recently added the Prusa’s i3 MK3S+ 3D Printer kit to the mix. Again, there are many options, printers, upgrades, filaments… choose wisely.
Let’s move onto what works, finding something that works for your printer, or future printer. I’ve maintained more of a ‘happy path’ as a hobbyist, less venturous and sticking to the PLA’s (Polylactic Acid) and TPU’s. Again, MatterHackers does a great job sharing what’s on the market – types of filament, sizes, brand, color. Dive in! Or maybe, expansion is on your mind, and you want to setup your own print farm – @ShopNation might be a great research to check out. Have options, which might be the biggest take away beyond testing or OEM/OEM filaments. Hey, as a hobbyist, saving some cash is good thing, there are thousands of upgrades on the market, same for the number of printers, filaments, parts, boards etc. What I’ve found through various testing methods, settings, set ups, printers and more, has been more about what works, the ‘success’ metric here. Consistency, fit/finish – quality over flash, speed – quantity. Take for example, and why perhaps I’m writing to you now, Duramic 3D TPU is just not working in the Ender 3 Neo Max rebuild. Teardown, rebuild all updated, same result, so, again, time to make a switch.
The switch, I’m referring to here (moving from generics to OEM) worked on the PLA side of the equation, may be a correlation perhaps, and not causation. I believe that’s the value here. A handy lesson here, might be to continue to test where it makes sense – remembering “correlation does not imply/mean causation” ((Shout Out)) Find more about Mr. Glickman on his personal website or faculty website, Mark Glickman – Senior Lecturer in Statistics, Director of Masters Study.
If you want to learn more about filaments, do your research, please do look into – MatterHackers, All3dp – Filament Finds and/or @ShopNation…
I’ll leave you with this, try what you can afford… what you can afford to discard, test and worked to fine tune your printer. Words of encouragement ‘leave no product stone unturned’. The goal is to produce high quality, consistent and clean prints. Find something that works 80% of the time, the old 80/20 rule. PLA is a bear to tweak and maintain, so is TPU and the ~14 other materials including metals, carbon fiber, wood, nylon. The application is endless, from starter to full forge, high-strength, commercial production. Focus in on settings, adhesion, extrusion temp, nozzle temp, surface tension, drives – pushers… And so it goes, testing is our motto/mantra, testing has become a constant when finding something that works, good over bad outcomes… so, test them all. Checkin from time to time, new posts are created daily, we will cover the Prusa tests, Creality TPU, Polycarbonate and PVA (Polyvinyl Alcohol).
Have fun, cheers
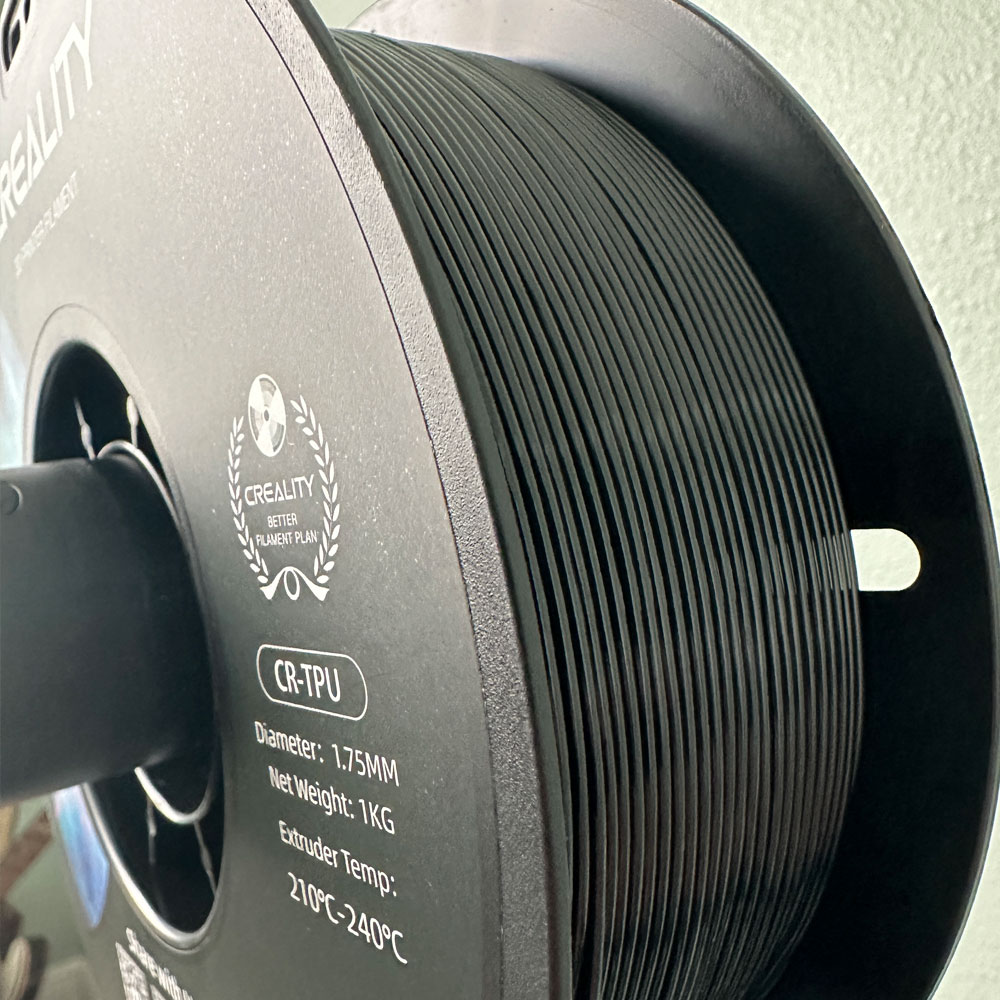
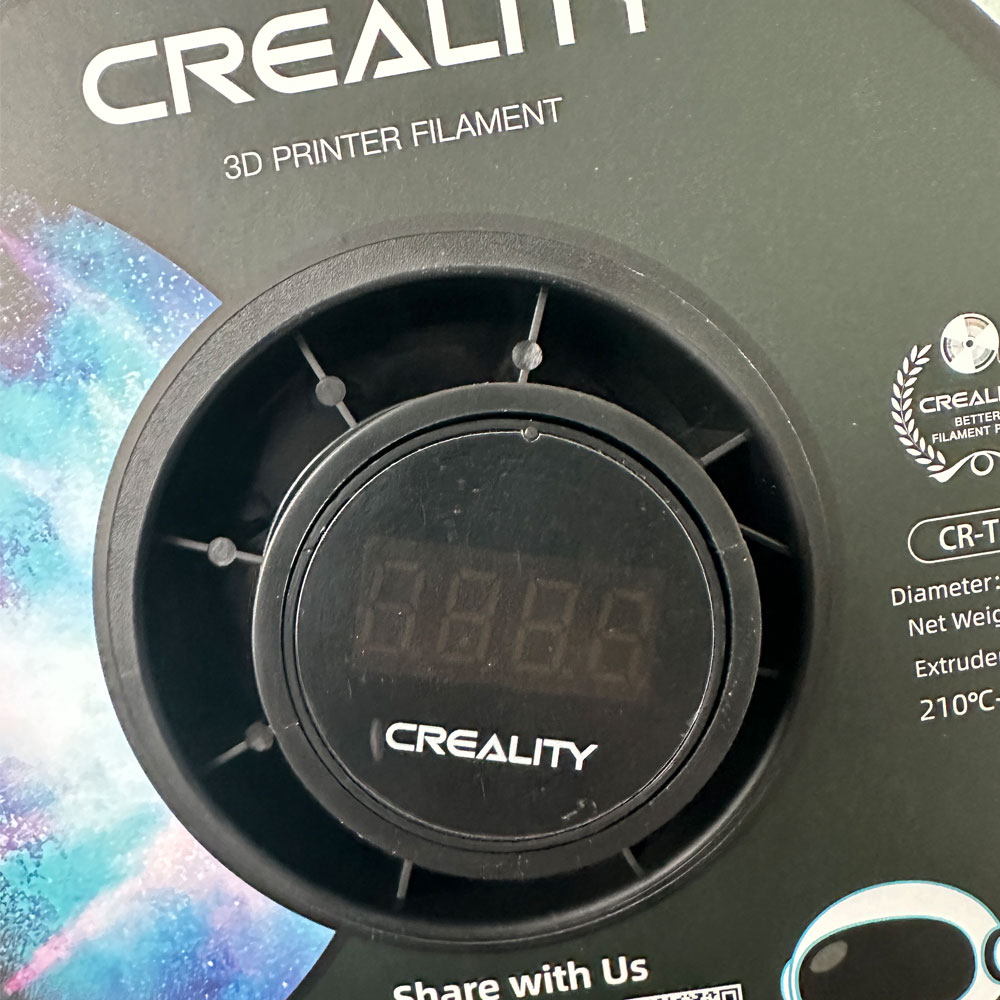
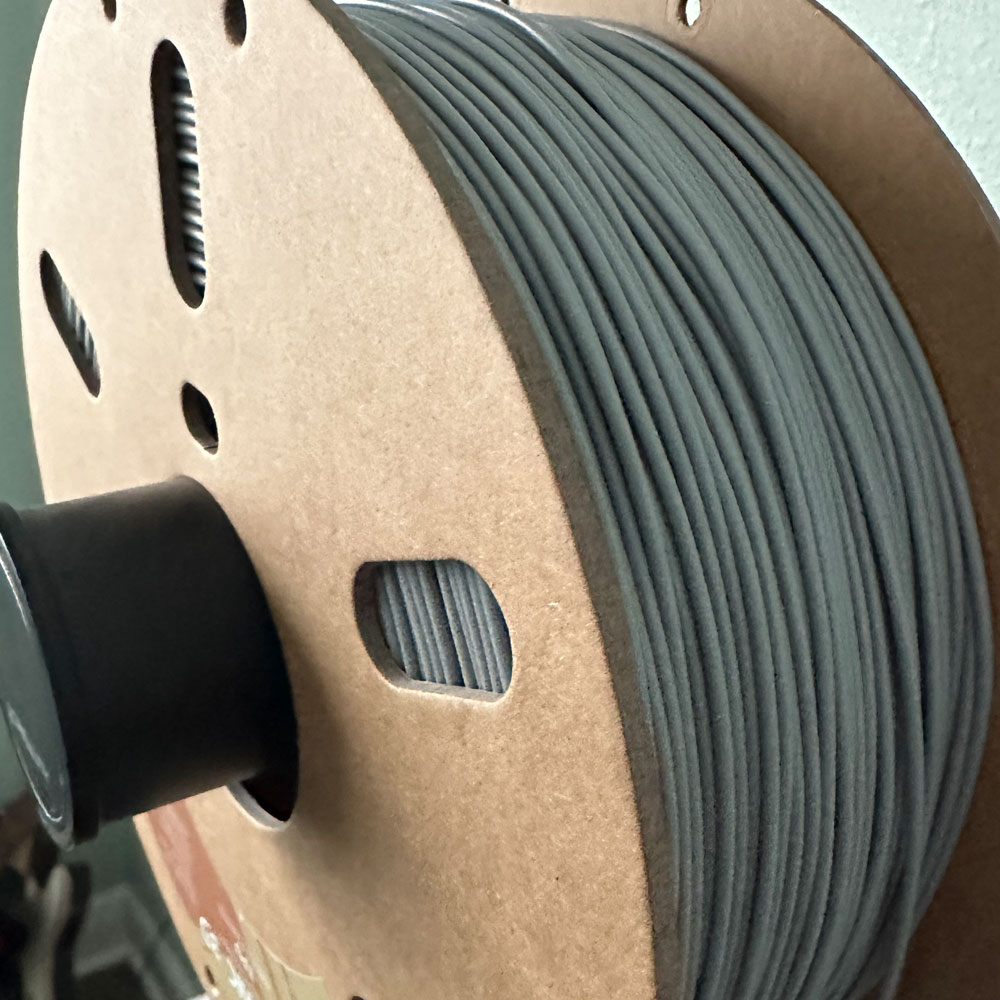