Review The Show 23
Let’s discuss MLB The Show’s, Road To The Show
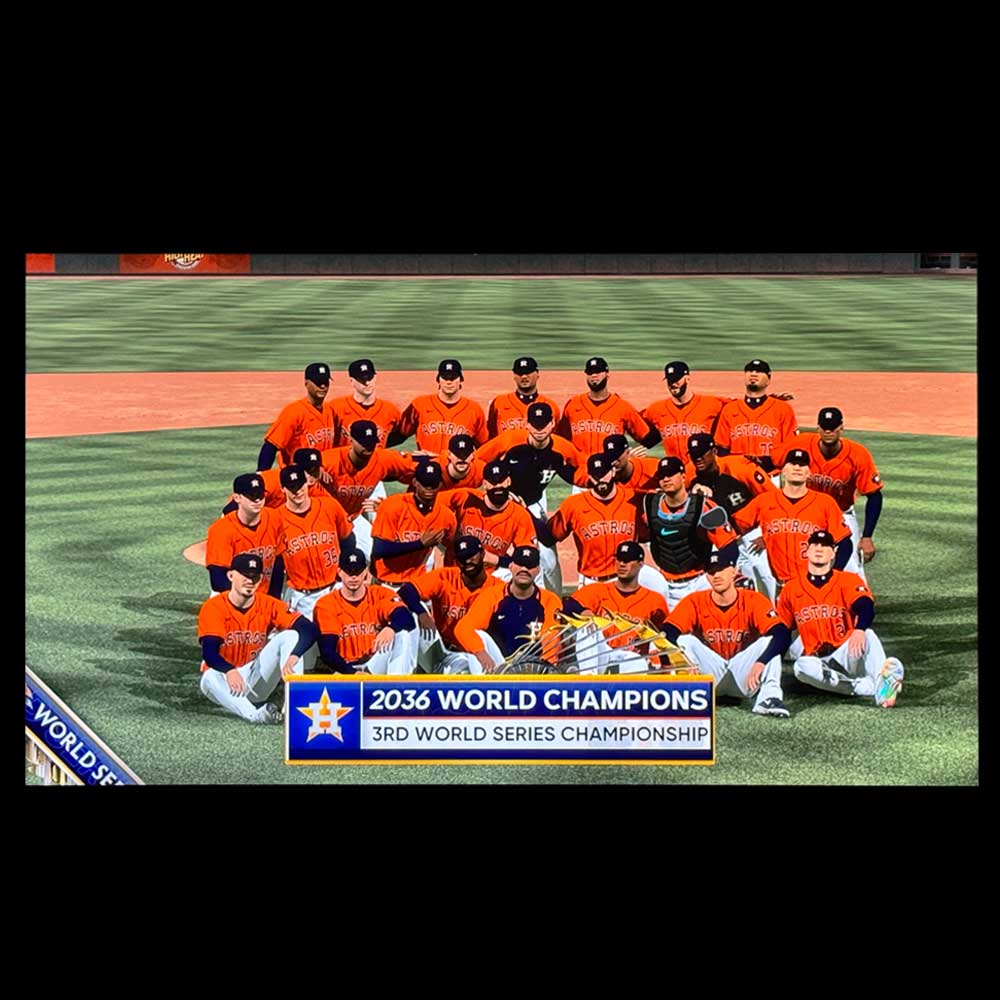
Lab Work – Review – MLB The Show 23
Grew up playing baseball, dreaming of the big leagues “bigs’. MLB The Show 23 Video Review starts with a similar dream sequence where your character dreams of being drafted and playing baseball professionally. Get drafted.
As a huge baseball fan at heart let’s talk about MLB The Show 23 first. The game has been out for a year now, with 24 being available for some time since it’s initial release in March 2024. From a demand perspective,MLB The Show 23 is currently discounted ($29.99). Don’t miss out on this great game for the price. You can also pick up MLB The Show 24 at its normal price ($69.99). Pricing may change, assume it will. This article was written as seasonal/quarterly pricing dropped. We will cover that game and the upgrades in the next month or two.
For us, there are a lot of pre-play modifications, design and character modifications, customization options, such as scanning your face for those who want their player to look like themselves virtually. Special character features are included in MLB The Show 23. We skipped around, and created one of the biggest virtual players (similar to an Aaron Judge type character),and jumped into the game. If it’s your first time playing The Show, keep it simple. You can always update and modify your character as you continue to improve their ball skills and perks. Those who want to modify their avatars can do so. As I mentioned, you’ll keep modifying your player throughout the game.
Character, check. Position, second base, check. Team, Houston Astros, check. Goals, make it to the Majors, an All Star Game, Home Run Derby if possible, and a Championship. Let’s play. Teams will come and go, but in hindsight. I wasn’t focused on one particular team, or a favorite team. So, Houston it is, starting out in their Double AA affiliate, the Corpus Christi Hooks. And onto the Triple AAA affiliate, the Sugar Land Space Cowboys, as a first baseman. I was having trouble with throwing mechanics, so it made sense why I was ultimately moved to Tampa, once I made it ‘To The Show’.
Keep it simple, second base, play as much as I can. Learn how to hit, different areas of the field, ‘stealing’ and general feel for the game. Don’t over look the game packs as I did. Build your players skills, talents, equipment list and play often. Another pointer, try and develop relationships with other players, when at bat, or batting, look around to see who is on base; look to drive in those players; effectively furthering the relationship with players on the diamond. Same can be said with hitting, learn the mechanics, pitches (pitch horizon, target zone and pitch types. We will keep this above all the hitting and pitching details. There is a lot there as I said above.
Ok, formal play, we play our way through the first season, limited missteps, but throwing remains a problem. Note, you can go back to the main screen and choose to play ‘old school’ baseball mechanics. This limits controller bindings, limiting buttons, pad and sticks/bumpers. Back to the game. We moved up to the Big Show in our second season, not for long… the move from Houston to Tampa came fairly quick as expected. What I didn’t expect was the move from Second to First Base. Perhaps I should’ve. So, first base it is, MLB team, Tampa Bay Rays.
So, this is where I spent a lot of my time building my characters skills, stats, perks, equipment and more. Give those in game challenges a go, fail fast. Packs are going to help your characters specials or influence player type. My player type is a home run ball hitter, going yard’, a Great Bambino type (*for you Sandlot Super Fans); a super contact hitter. Power comes later. Stealing is a bit dry here in the early game play. My player just doesn’t have the speed or the right timing. Get the practice in while you can, like my fielding, stealing is some what of a mystery (I stay away from later in the game).
We celebrate our first All Star games on both the AA and AAA affiliates, and get into a good pattern of limiting field errors and going yard (hitting home runs).
We Continue with In-Game challenges and Practice
Things I wish I knew to start: equipment packs, open those asap. You can earn packs by completing the in-game challenges, do so. Two, once an action has been selected, (meaning the choice was made to play a game vs sim a game)… actively participate in in-game skills challenges. If you don’t know what you’re doing, before hopping into the game, take some practice time.
Practice time, helps with all around skills, remote control stuff (how to hold it, familiarize yourself with the controls, what does what etc.). You’ve really got 4 to 5 seasons to move onto another team, play often and try to hit home runs.
Moving on, so, 4 years with the Rays, following the 2 first year seasons. I will maintain a lookout for other teams interest, to see if we can create a super team. For now, Tampa is the team. Also, the team where we go on to win the first of three World Series Titles.
Two More Titles
Two titles won with Tampa, separate seasons, the second coming late in the middle third of my career ~88 – 90 range of experience points. Riding out the first WS and the rookie contract, no takers, we whined up with the Durham Bulls in the off season following contract arbitration. Missing out on a max deal, and not knowing how the game ‘functions’ just yet.. meaning expected outcomes vs moves that might take you in the direction you want to go with your career.
Missed Max Deal, Picked up by the Astros, Durham Bulls.
This is the time, where game play, or playing (playing each game vs simulating a game, month or season) makes more sense. The cutscenes will keep you in line with game expectations and outcomes, if you so choose to pay attention to those scenes. Our first Home Run Derby was a flop, while the All Star game was a mild success. Not my best game, but sticking to the 3 for 4, multi-home run achievement per game. A divisional MVP and a Second World Series. See images below here. I’ll post some of my next stint in a future post.. as I’m trying to keep this surface level content.
Astro’s Championship – WS Title 2
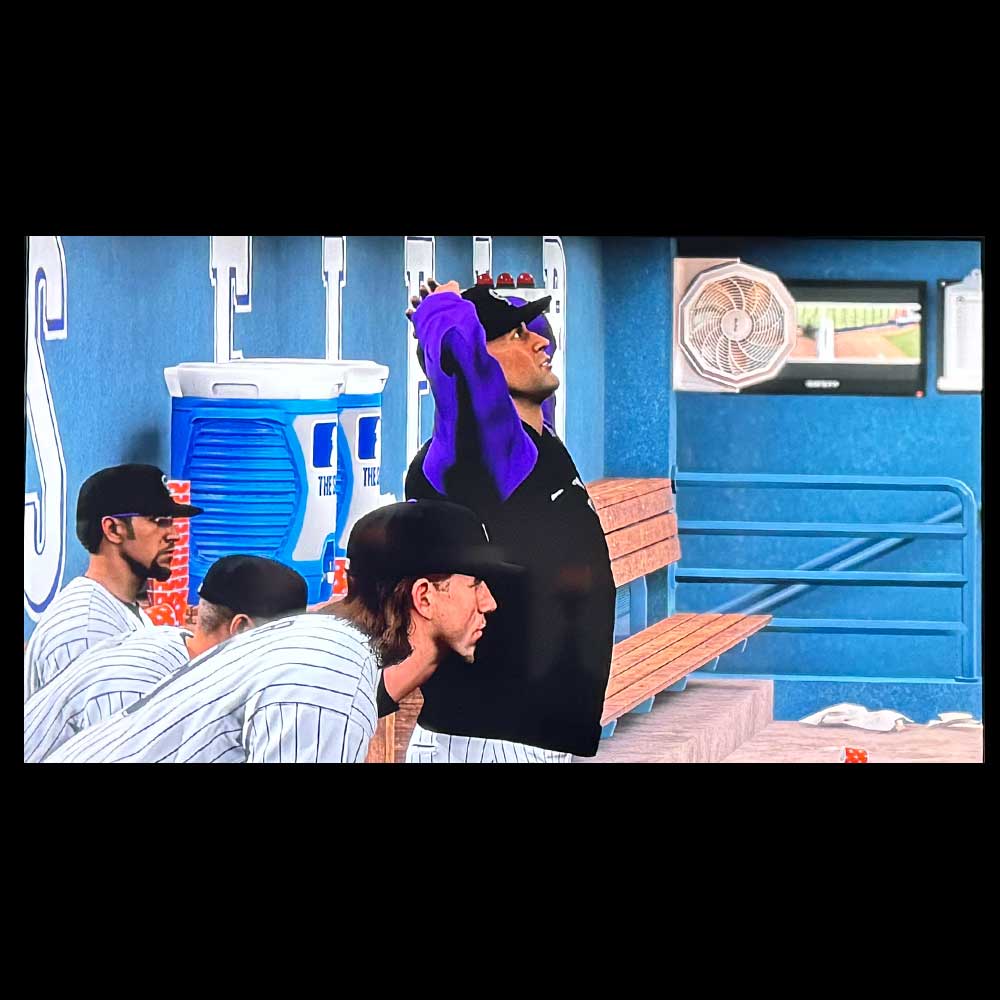
CO Goes Down
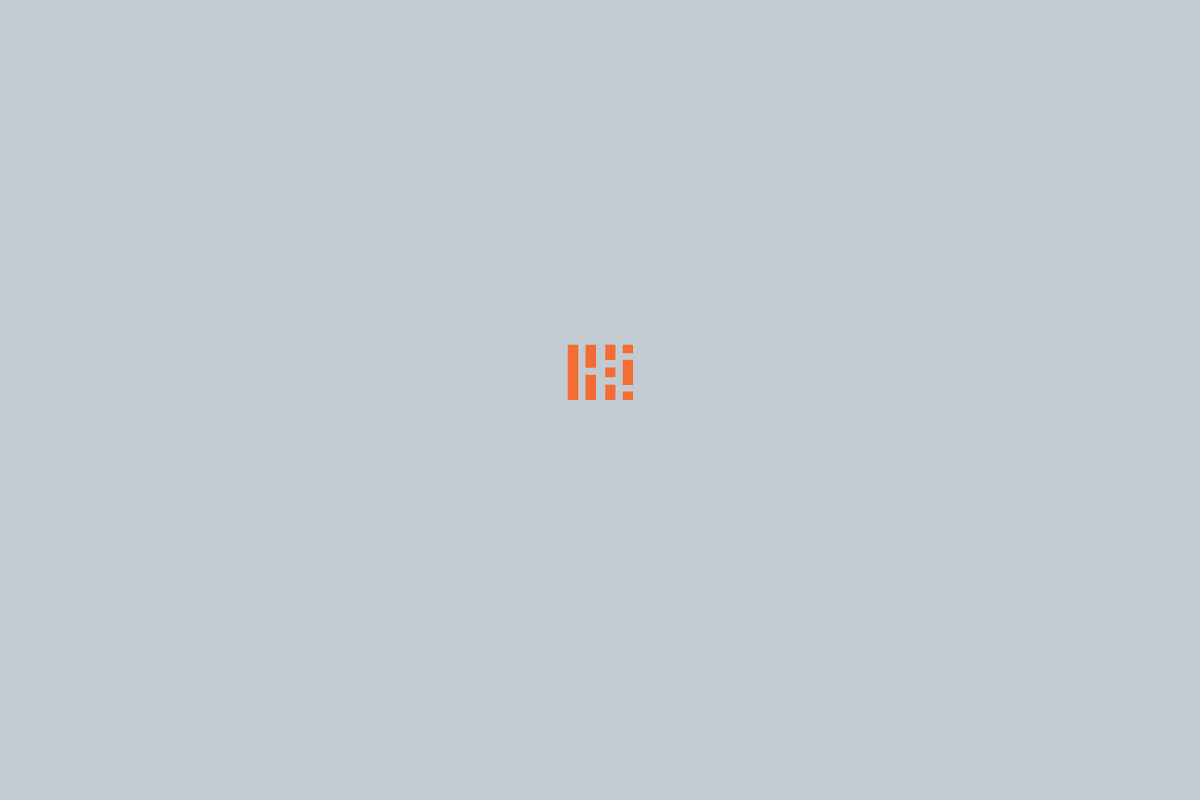
Championship Cut Scene
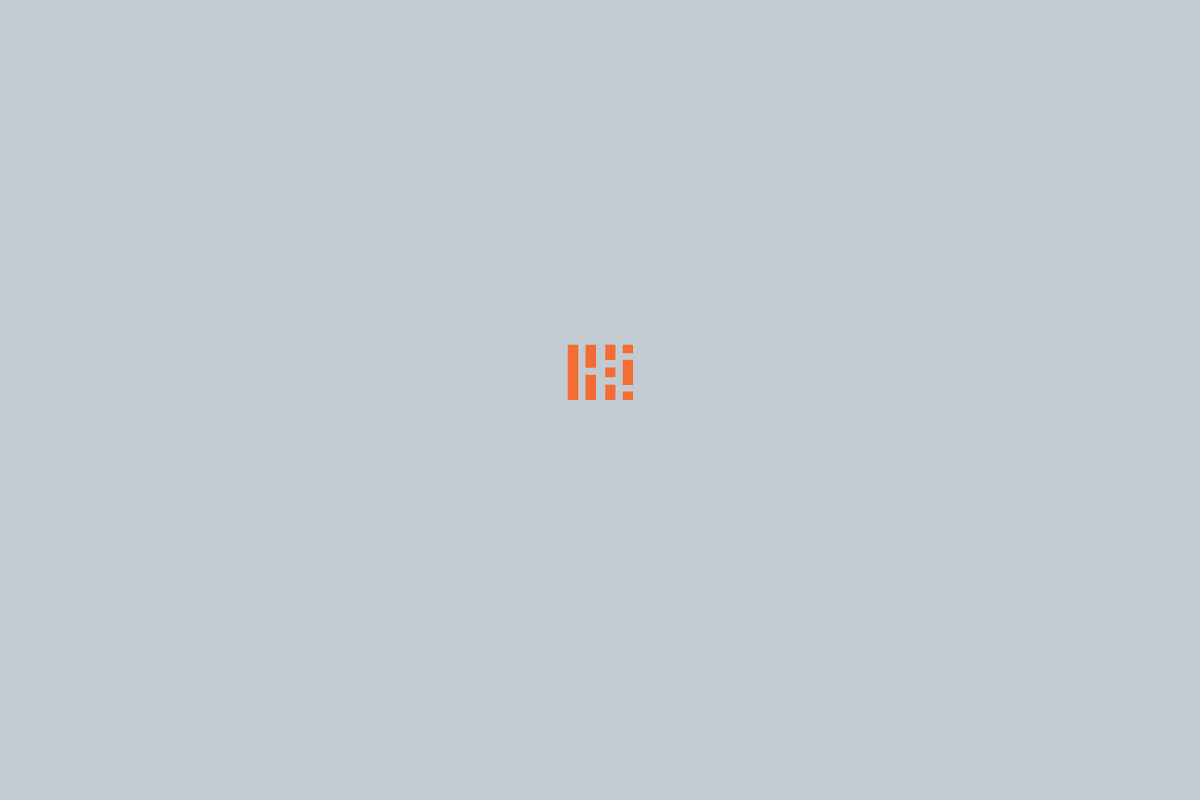
World Series Marker
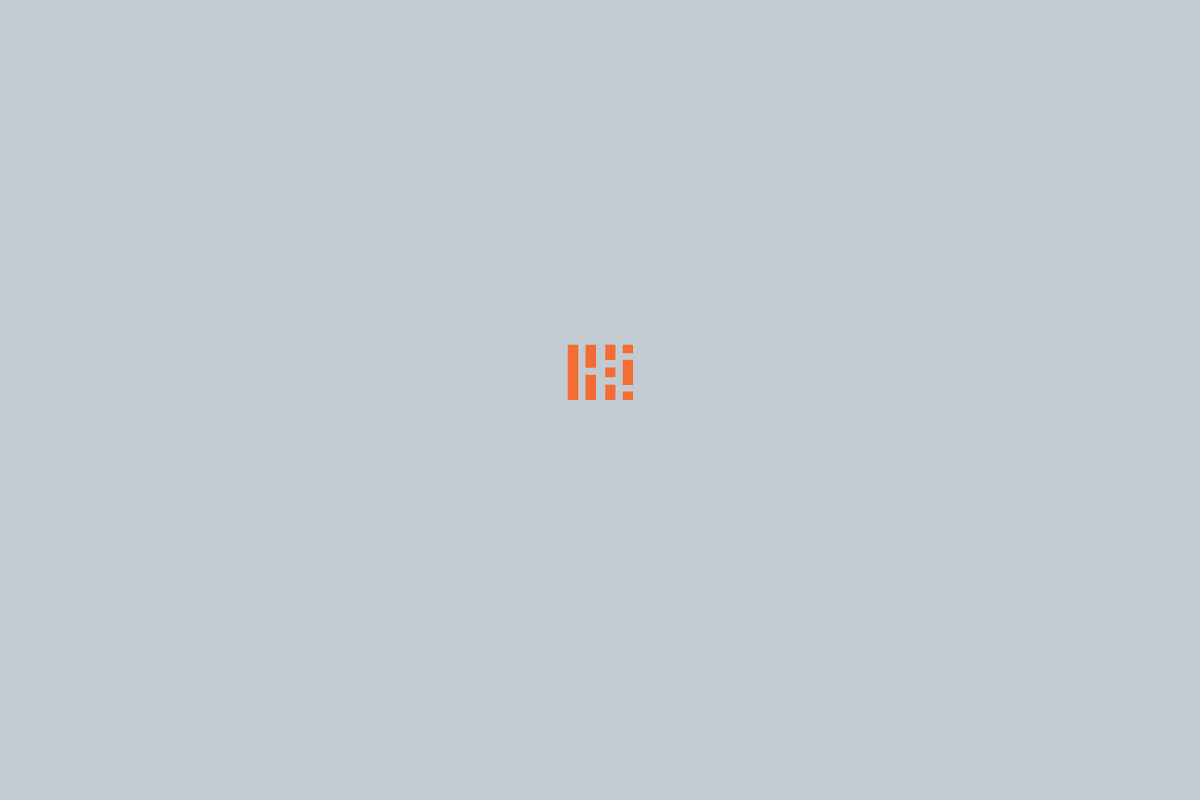
Player Champion
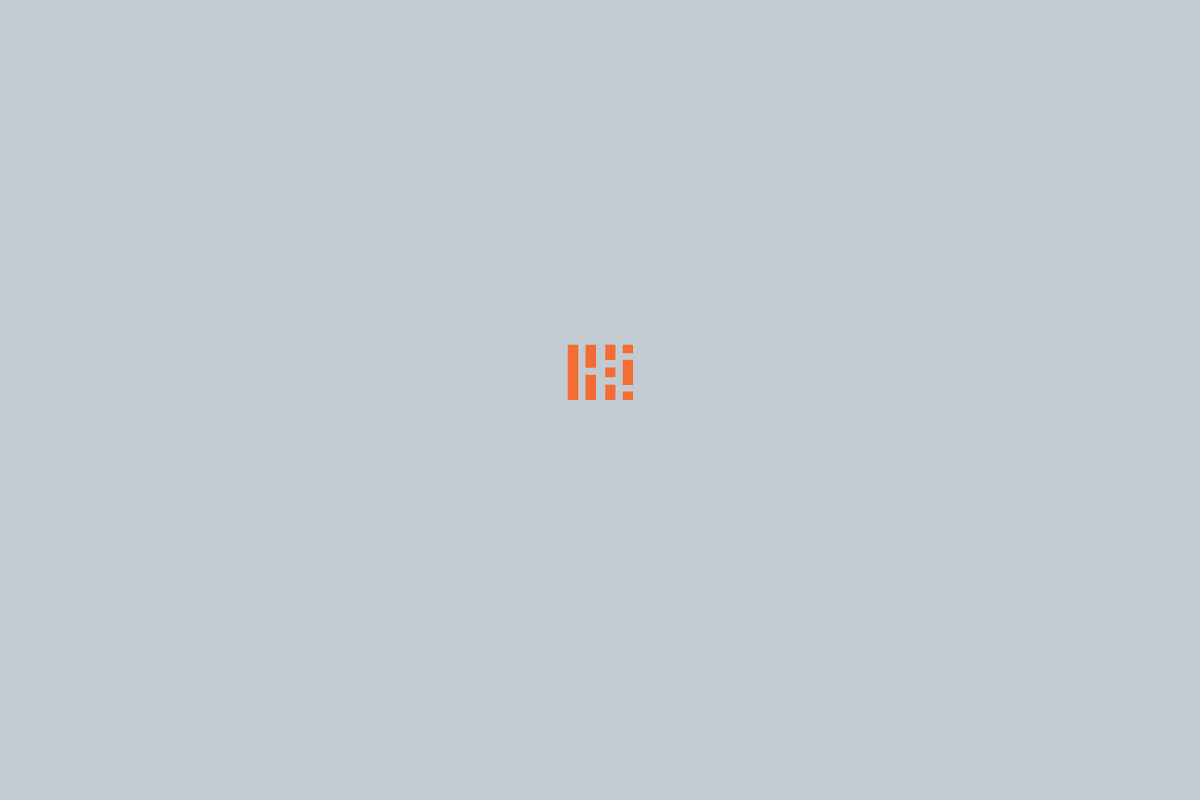
Commissioners Trophy
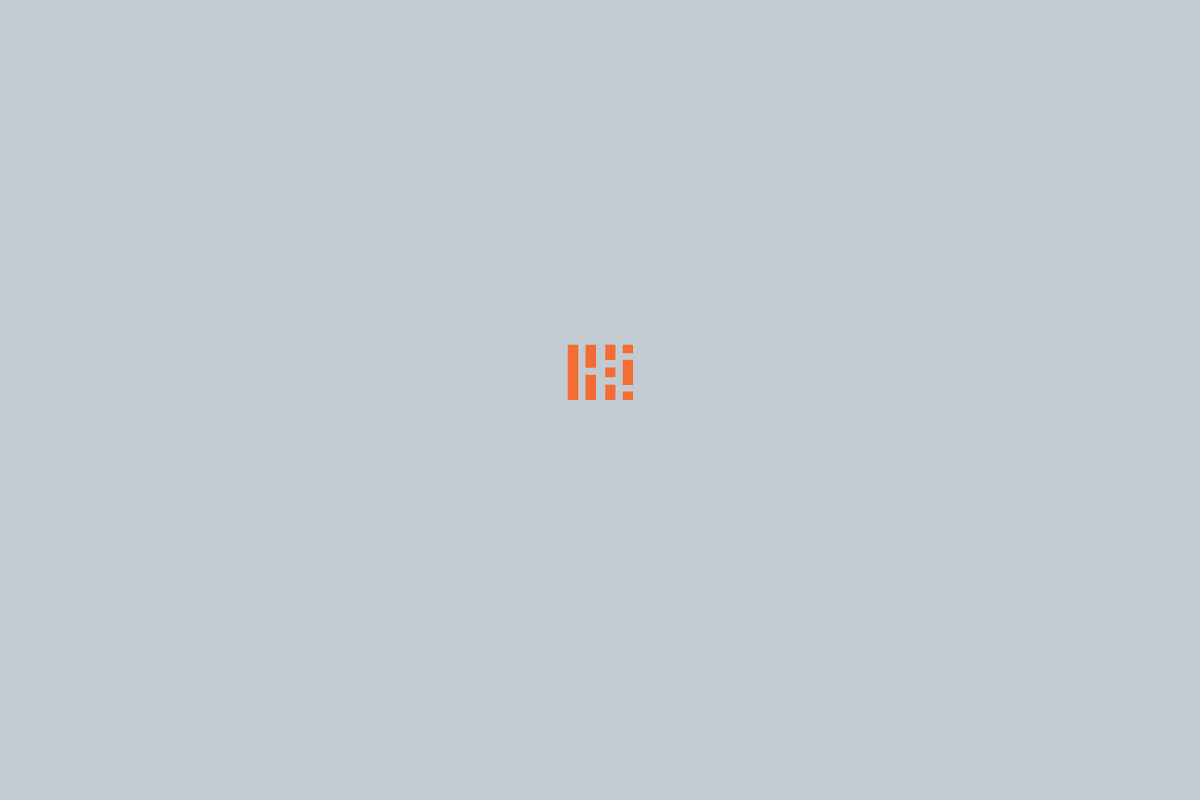
Cut Scene 2
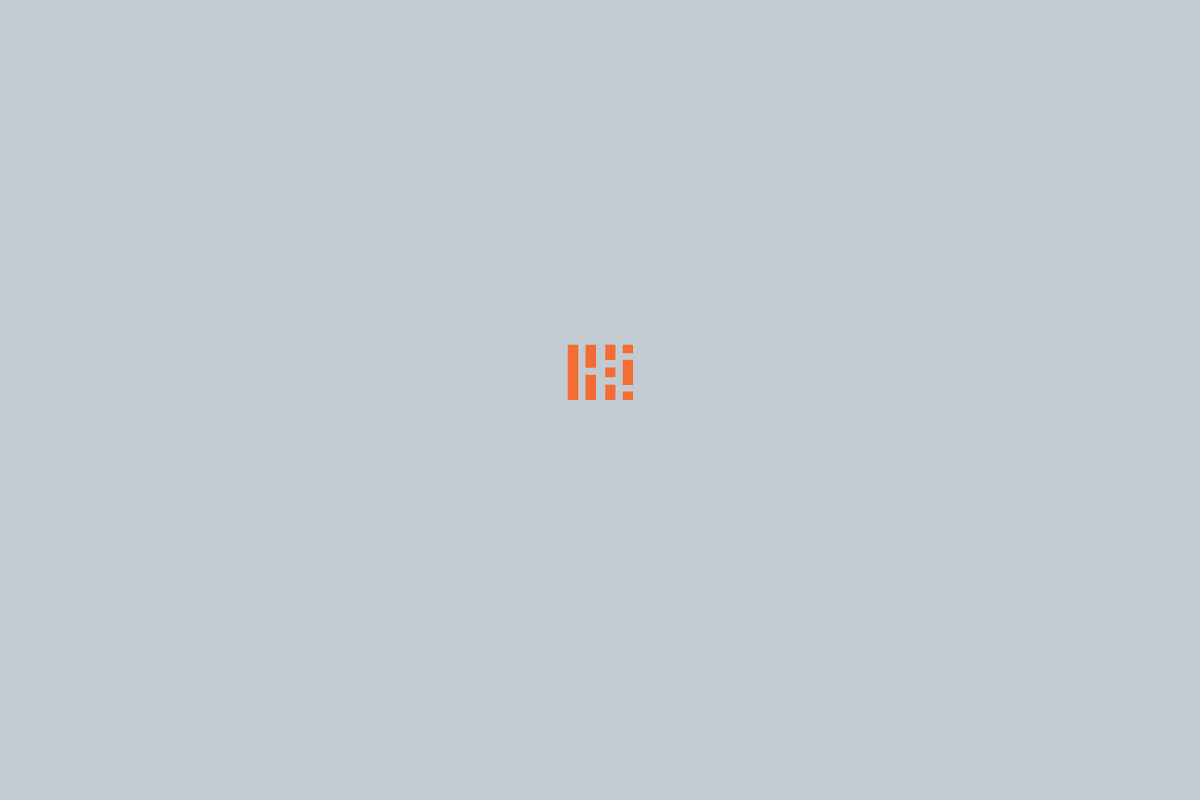
Raise The Trophy
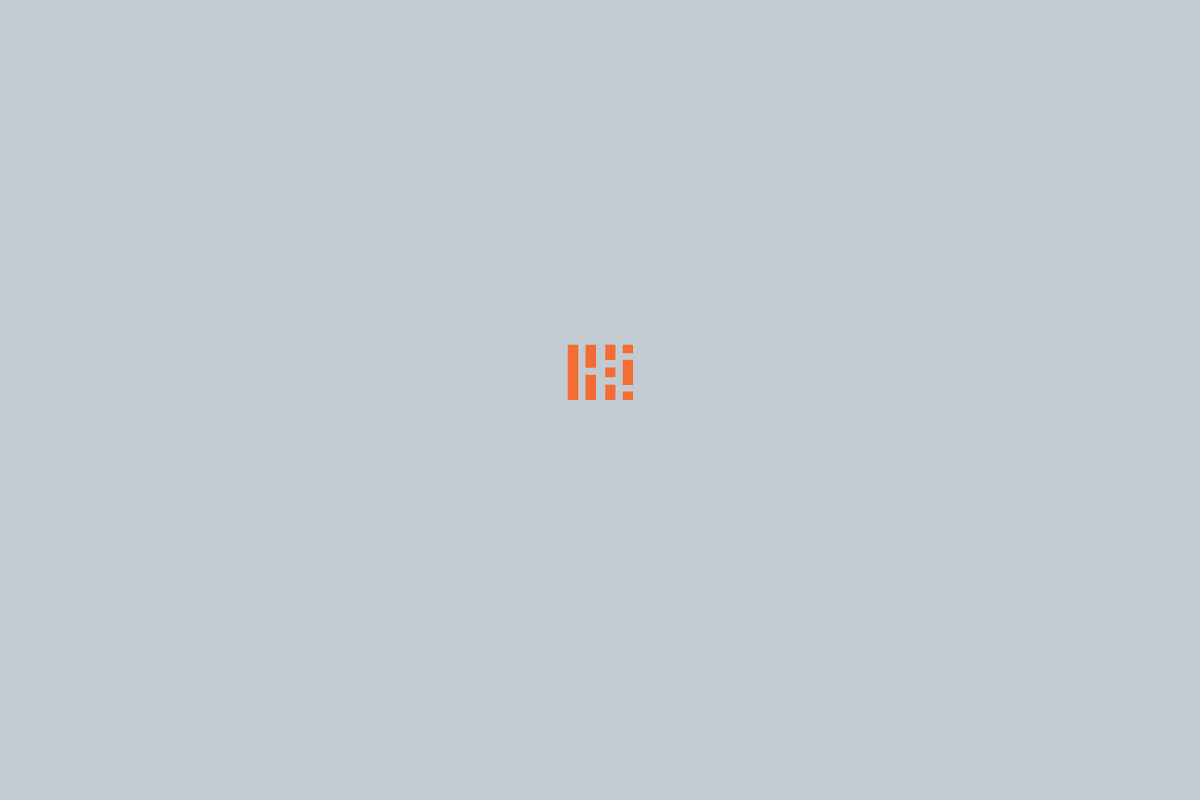
Team Photo
Let’s Wrap Up, Onto a 4th WS Title
The jump off point, late in my career, I want to win, best options are not on the table… so, spring ball is where I go. Missing out on a third max contract. Unfortunately, of the teams offering contracts – Brewers, Cardinals, Reds and Padres; I was not interested. Like before, we ended up choosing our next team, which came in the form of a pin-stripe uniform. The Yankees, love ’em or hate ’em, I was playing first base, max contract for 2 years, late in my career. Now at that 90-92 experience score level. Almost playing every game in the season, so, time will tell where the season ends.
Post Championship – Agent/Player Discuss Options
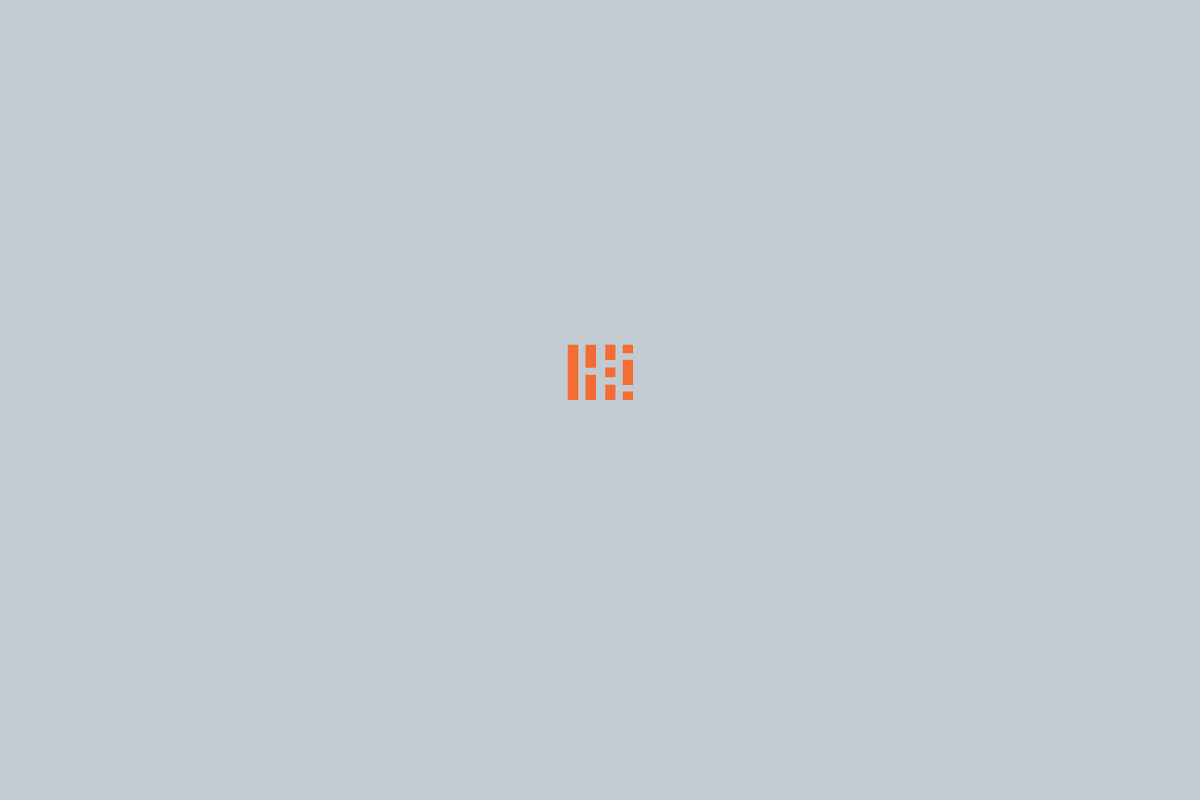
Peavey Talks Experience
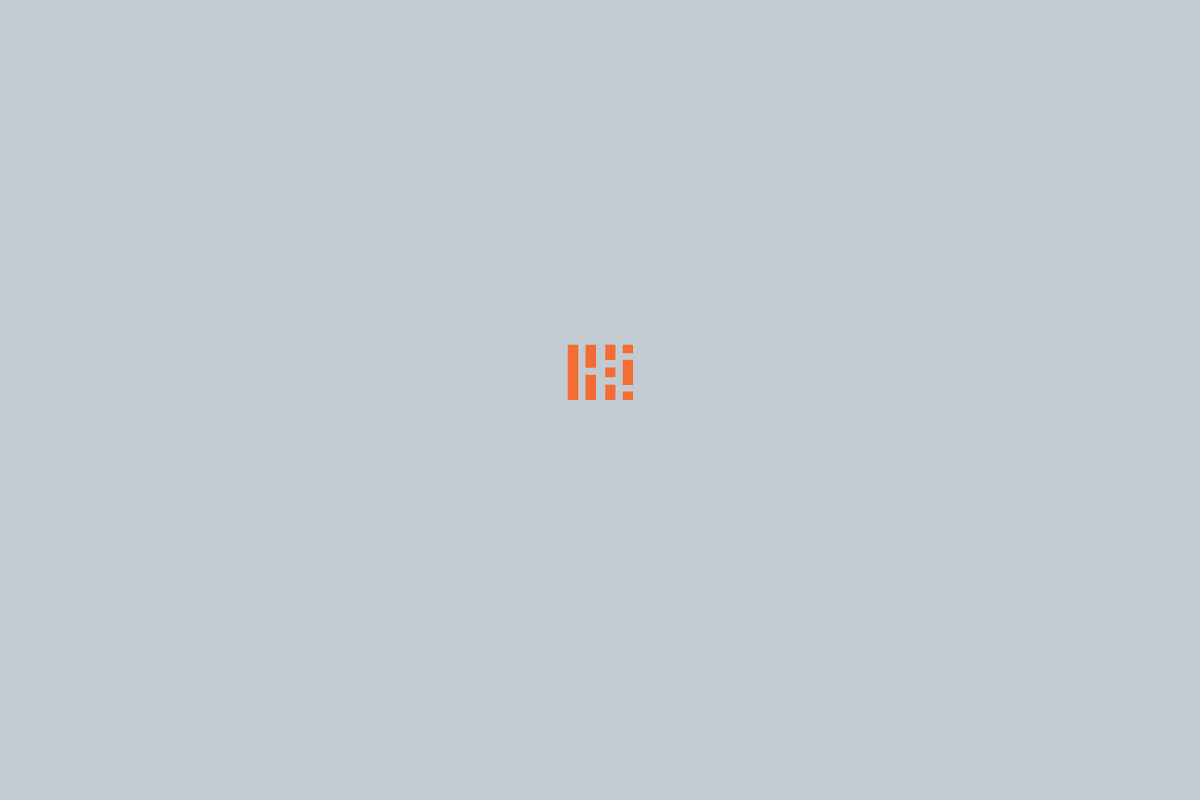
Pena’s Take On the Title
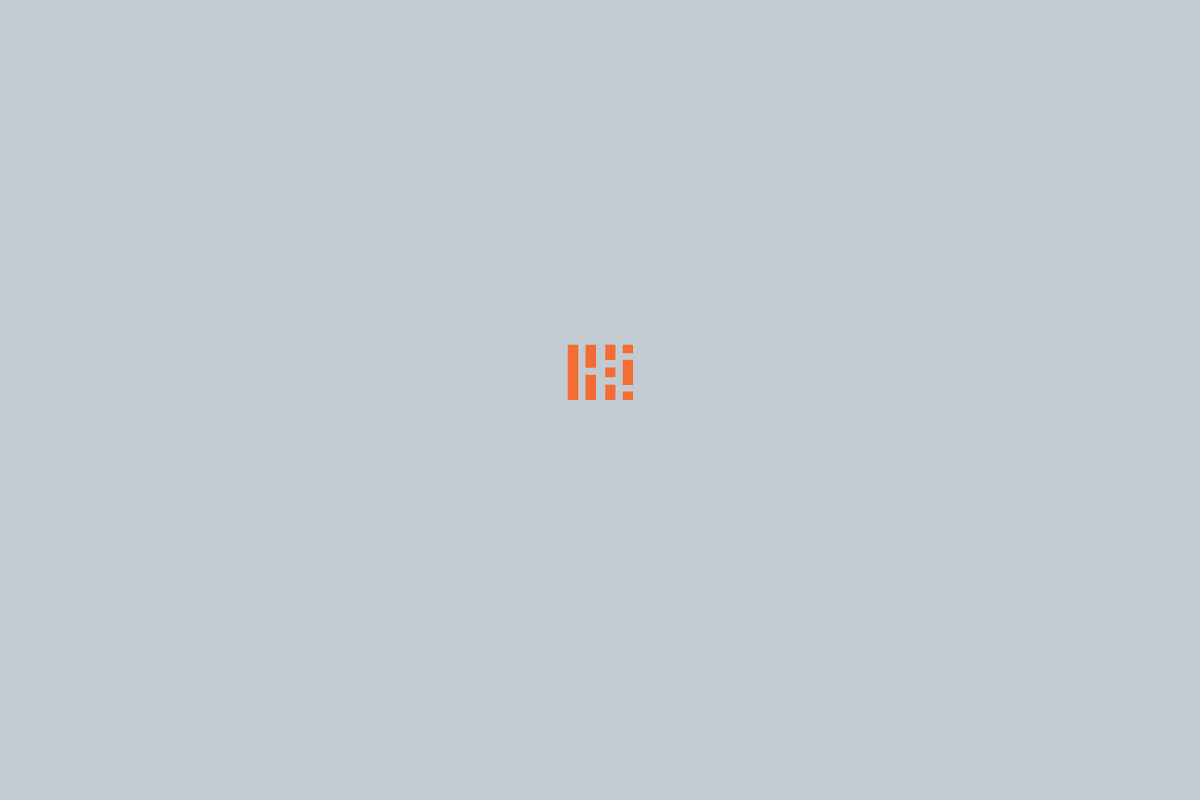
TPost Game Chat
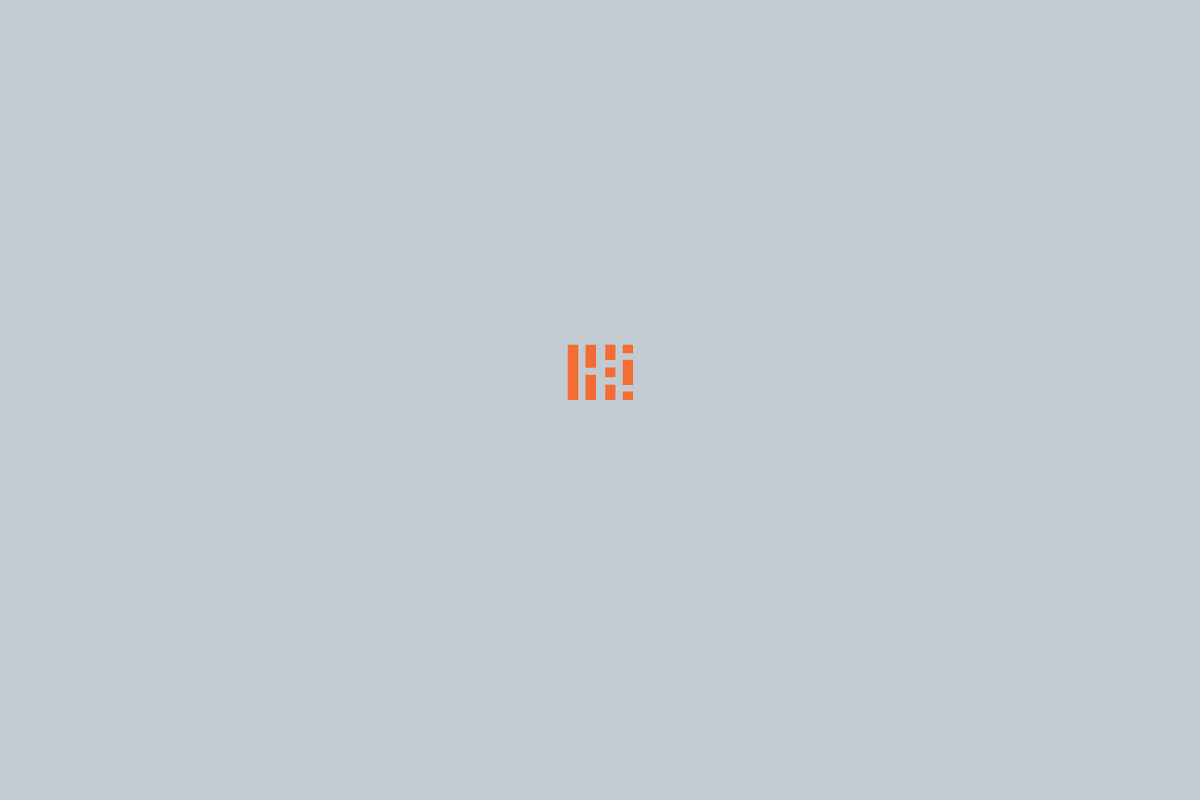
Arbitration
Quick ending here, we wrap up with our agent/player discussion, and what’s next for the veteran. Ultimately choosing to move on, the article closes with the ‘pursuit’ of a fourth go around; a 4th World Series. I missed out on a second in Houston, but that’s fine. I’ll come back to the game in the next few months as a new player, maybe a lefty pitcher; a Dennis Eckersley or Randy Johnson type – super tall, lanky, sub-ball thrower, throwing heat. So, I’ll leave you with this – keep it simple, max out your player, play often, sim less if you can. Win those card packs, before you choose which item to select, use triangle to preview value. You can always dump players, doubles or discard traits you don’t want onto the online marketplace. Yes, you can sell cards too. Finally, increase your power, contact, speed and equipment.
Lastly, check out more videos like like, the original NES Baseball game shared via @worldoflongplays.